Boeing Additive Manufacturing enhances capabilities at Auburn site
The BAM Fabrication Center will help accelerate efforts to manufacture production-qualified 3D printed parts
Boeing continues to invest in the future through cutting-edge, additive manufacturing technologies to unleash possibilities and leverage 3D printing in the design and manufacturing of parts and tools.
At Boeing’s Auburn site, the Boeing Additive Manufacturing (BAM) Fabrication Center was established to further the company’s efforts to develop repeatable, stable and reliable additive manufacturing processes, and meet certification and qualification requirements to increase additive manufacturing production of fly-away parts and systems.
“This was placed in the ‘heart’ of the Boeing Fabrication Division in Auburn to use synergies across the site in order to accelerate the qualification of additive manufacturing production,” said Tamas Havar, director of the BAM Fabrication Center.
Additive manufacturing — also known as 3D printing — offers reduced cost and weight through design and production of lightweight structures with reduced assembly and faster production. Additive manufacturing enables highly complex parts to be made with added functionality that cannot be manufactured traditionally.
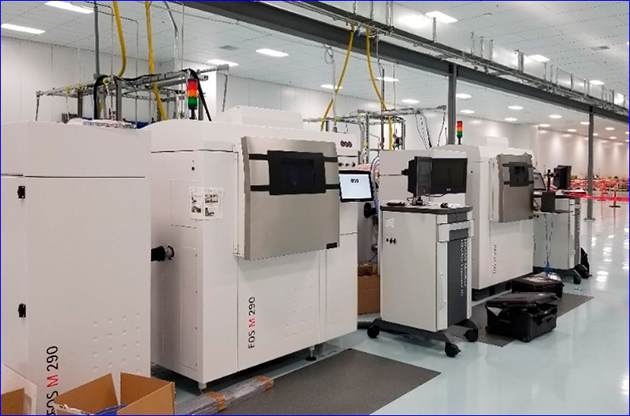
Boeing uses additive manufacturing to accelerate innovation and create value by improving quality and costs in products, enhancing efficiency and safety in operations, and collaborating with customers to develop additive manufacturing solutions.
The BAM Fabrication Center, which completed construction in spring of 2020, has the following capabilities:
- Metal powder-bed printing in aluminum and titanium in a 32,000-squae foot print room with nine machines and laboratory equipment.
- Large polymer printing for tooling on a Large Scale Additive Manufacturing printer that’s located in the manufacturing factory adjacent to the print room. The LSAM has a 20-foot print bed that can print tooling as large as 10 feet wide, 20 feet long and 5 feet tall.
- Polymer printing in a 4,500-square foot space with 13 fused filament fabrication (FFF) machines and post processing capabilities. They polymer FFF machines can print tools and parts, such as ducts, brackets and interiors.
- Office space in a mezzanine above the factory floor and conference rooms to drive increased collaboration and integration between the additive manufacturing engineers and machine technicians.
By Paula Horton
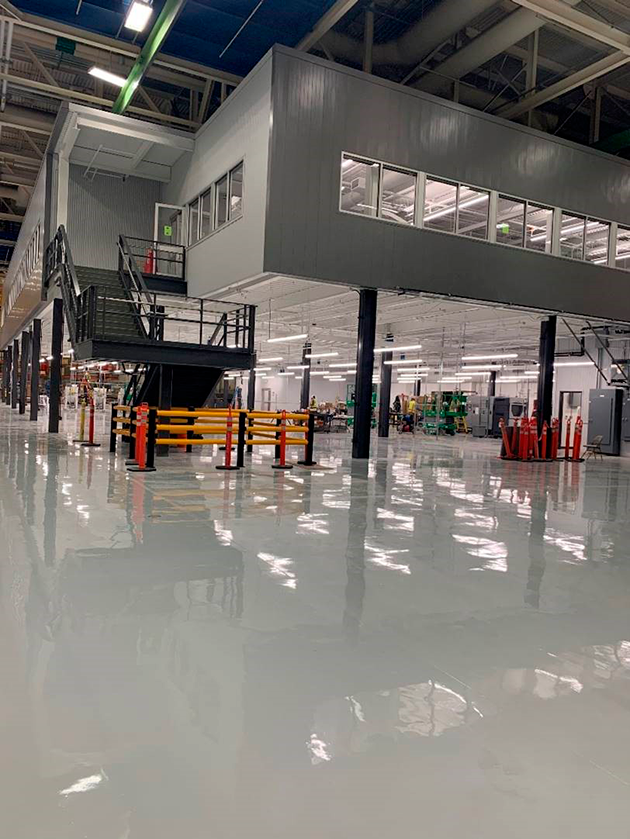