Picture-perfect welds
Senior welders join with Boeing teammates to solve a pressing ergonomics issue
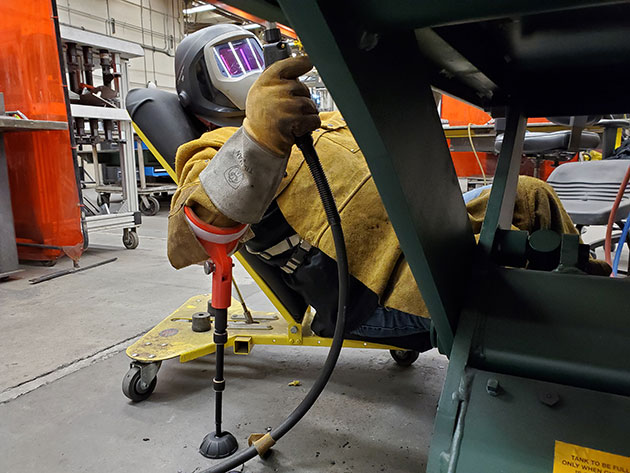
Boeing ergonomists such as Miriam Joffe help Boeing wage war on ergonomics injuries every day with support from those who experience the injuries. Ergonomics-related injuries can occur to the musculoskeletal system, including muscles, ligaments, joints and nerves, when job requirements exceed the worker's capabilities.
“Many of the early warning signs that our employees experience can be eliminated through the implementation of appropriate ergonomics principles,” Joffe said. “And where they can’t be eliminated easily, we may look outside the box to modify off-the-shelf items or custom design a specific solution to reduce the risk for injury.”
One recent example was a demonstration she had seen involving a monopod, a single-legged, collapsible camera supportwhich are often used by sports and wildlife photographers. Joffe thought this might have an application for welders.
Like their counterparts across many industries, welders suffer from neck, shoulder and back musculoskeletal disorders. That’s why welder Doug Beal is on the constant lookout for ergonomics improvements.
“I don’t want the young welders to have the same injuries my partner and I have,” Beal said. “Long-lasting, sometimes life changing, injuries are avoidable with smart ergonomics. And any tools I develop to help with that will outlast my time here at Boeing.”
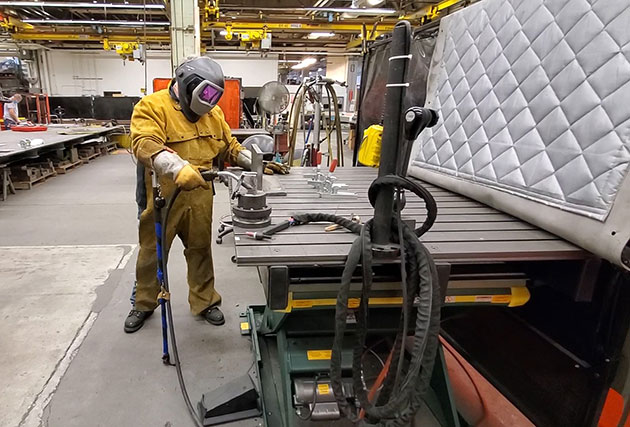
This isn’t Doug Beal’s first time creating a tool that can help welders. In 1995 he developed the universal weld positioner for duct parts, which works on more than 1,400 duct part numbers.
This time, the solution the team delivered is simple and surprising: a monopod with a custom arm support, lined with a fire retardant pad, that attaches to the forearm and has a weld assist strap attached. The monopod gives the body and arm a point of stability and a place to rest the arm when there isn’t a table or other means for support.
The device also reduces back, shoulder and wrist strain that may result from holding a heavy torch, welding tool and weighty cable in a static position while engaged in precision work for long periods of time.
“The best picture-perfect welds come when your hands are free and supple,” Beal said. “This tool improves weld quality and reduces rework, in addition to protecting people’s bodies.”
Two tools have been created: a monopod for welding while standing, and a mini-monopod for welding while seated or lying down.
“This was a team effort – I took what engineering created and made it specific for welders” Beal said. “Dave Smith, Miriam and I made a dream team!”
By Jennifer Hawton