First batch of 3D-printed face shields shipped out
Face shields to be used by medical professionals fighting the COVID-19 pandemic
As it ramps up its 3D-printing capability at a number of sites across the United States, Boeing has shipped out face shields for use by medical professionals fighting on the front lines of the COVID-19 pandemic.
The Department of Health and Human Services accepted the initial shipment of 2,300 face shields Friday morning. The Federal Emergency Management Agency will deliver the shields to the Kay Bailey Hutchison Convention Center in Dallas, which has been established as an alternate care site to treat patients with COVID-19.
The production and donation of the face shields is part of a larger effort where the company and its employees have been looking for ways to leverage their capabilities to help with COVID-19 recovery and relief efforts.
Howard Rolleston, an Additive Manufacturing Innovation Cell lead in Philadelphia, said “people have been coming out of the woodwork” to volunteer on the project.
“They’ve been fantastic. Everyone has been working together,” he said, adding that some have a personal interest. “The daughter of one of my co-workers is working as a triage nurse helping people who are getting infected with the coronavirus.”
Boeing has also donated tens of thousands of masks, gloves and other equipment to hospitals in need.
The 3D-printed face shields solution was developed by employees from Boeing Additive Manufacturing; Boeing Research & Technology; Boeing Defense, Space & Security; Supply Chain; and Boeing HorizonX, along with support from Accenture, hospitals and universities.
Boeing partnered with Design that Matters, a nonprofit group in the Puget Sound area, on the design, which includes a 3D-printed frame with an adjustable headband that allows a clear plastic face shield to be easily snapped onto the frame. Solvay, a longtime Boeing supplier, is providing the clear film for the shield. Its composite materials division has a long-standing relationship supporting all Boeing platforms for several decades. Another supplier, Trelleborg Sealing Solutions, is donating the straps needed for the adjustable headband. Trelleborg has a long-standing relationship with Boeing, providing sealing solutions support across all Boeing platforms.
The frames, headbands and shields are being shipped to the Boeing site in St. Louis, where they will be assembled and packaged for shipping.
Face shields and other personal protective equipment (PPE) have been in such short supply that some doctors and nurses have turned to swimming goggles and other homemade options.
Boeing is using additive manufacturing machines in St. Louis, Missouri; China Lake, El Segundo, and Huntington Beach, California; the Puget Sound region of Washington state; Mesa, Arizona; Huntsville, Alabama; Philadelphia, Pennsylvania; Charleston, South Carolina; San Antonio, Texas; Salt Lake City, Utah; and Portland, Oregon. Boeing subsidiary Argon ST in Smithfield, Pennsylvania, is also participating in this project.
Some sites where operations have been suspended have been given approval to contribute to the project. More sites will be included as additive manufacturing capability is identified.
The U.S. Food and Drug Administration authorized the face shields for PPE use by health care providers during the national emergency but has not cleared or approved them under its standard regulatory processes.
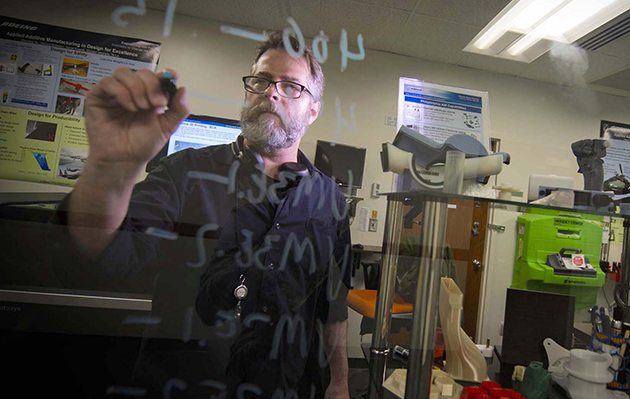