Response to COVID-19 PPE shortage showcases One Boeing teamwork
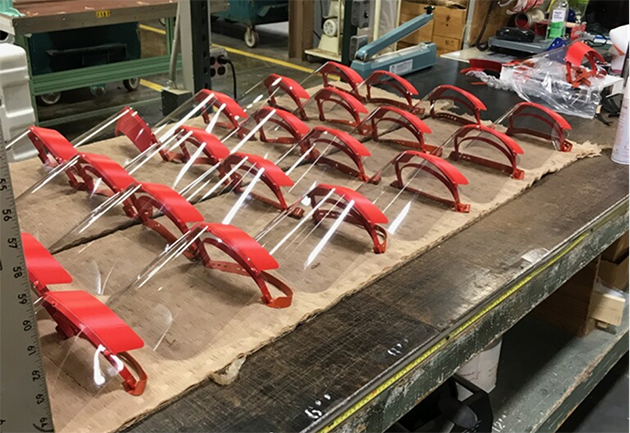
A three-month effort to provide personal protective equipment to health care workers treating COVID-19 patients shows how collaborating across Boeing for a common cause – and greater good – leads to success, leaders say.
Boeing Additive Manufacturing (BAM) spearheaded the effort to 3D-print 40,000 face shields that were donated to the Federal Emergency Management Agency (FEMA) and other organizations for distribution across the United States.
“Our intent was to address the emergent need with 3D printing while other technologies, such as laser cutting and injection molding, were tooling up their production lines for a higher rate production process,” said Melissa Orme, BAM vice president.
About 100 3D printers were activated at 18 sites to create the face shield frames. Employees from several organizations across all three business units and functions such as manufacturing, transportation, logistics, and supply chain also eagerly stepped up to help.
“Overall, it was a true passion for Boeing to be part of a monumental experience in our society,” said Vonda Davis, director of Metal Fabrication, who led the face shield operations in St. Louis. “There was a lot of focus on the capability of 3D printing and the innovation. But I also want to highlight how we worked together as a team to make something we don’t normally make in our production operations and have it be such a success in such a short time.”
It took about three weeks to go from concept to production and donation of the first shipment. That in itself was a significant accomplishment in a big company like Boeing, leaders said.
“There was a real strong sense of pride that we were able to move so quickly,” said Nick Mulé, director of the BAM Intelligence Center in El Segundo, California. “It was just incredible and it really shows where 3D printing can be beneficial for a rapid response to go from concept to having something in your hand in a short amount of time.
“The key to our success was the willingness of everyone wanting to help their respective communities and the open communication,” he added.
Boeing suppliers also stepped up to help. Solvay donated the clear plastic film for the shield, and Trelleborg Sealing Solutions donated the straps for the adjustable headband.
In addition to all the sites printing the frames, two sites handled the water-jet cutting of the clear plastic face shield that snapped onto the frame. Everything was shipped to St. Louis, where teams of production employees worked before or after their regular shifts to assemble, clean and package the face shields for delivery. Production areas were set up in three buildings in order to ensure physical distancing and safety.
“We had a waiting list every session. Everyone was really passionate about it and wanted to help. I don’t know if I’ve ever been on a team that was so collaborative,” Davis said. “I was honored to be asked to lead this effort in St. Louis … and I really enjoyed doing it because it was my way to help during the pandemic.”
Note: The face shields provided by Boeing have not been Food and Drug Administration cleared or approved. The face shields have been authorized by FDA under an Emergency Use Authorization (EUA) for use by health care providers as personal protective equipment. The face shields are only authorized for the duration of the declaration that circumstances exist justifying the authorization of emergency use under Section 564(b)(1) of the Federal Food, Drug, and Cosmetic Act, 21 USC 360bbb-3(b)(1), unless the authorization is terminated or revoked sooner.
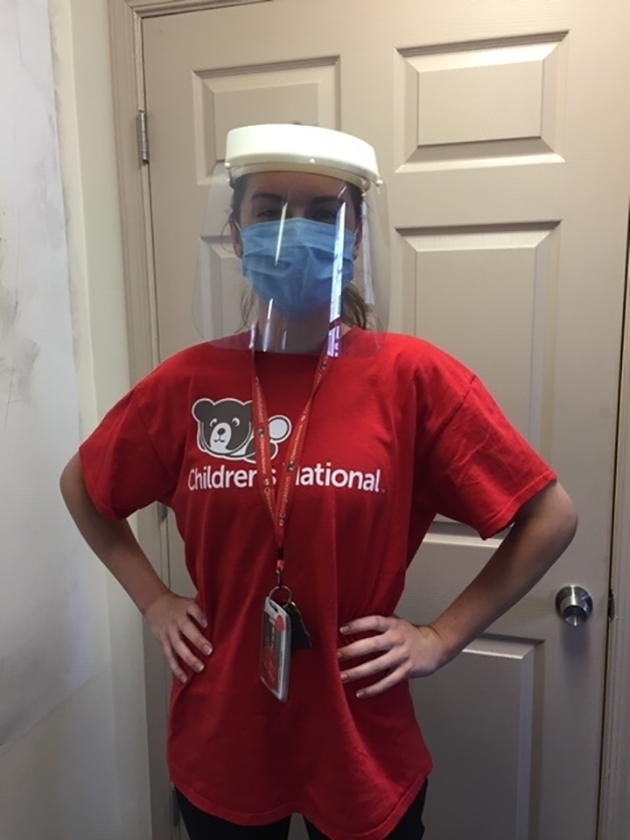