Performing under pressure
Successful composite cryotank trials mark an important leap in materials technology for space applications and sustainable aviation.
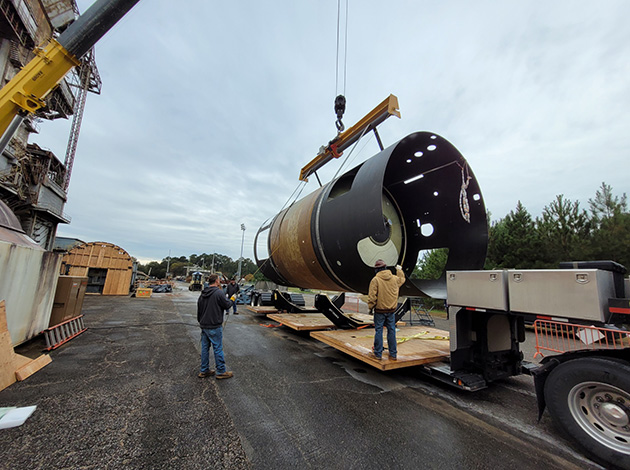
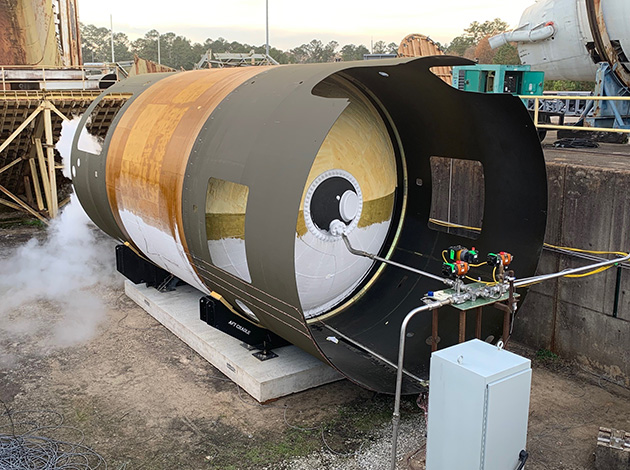
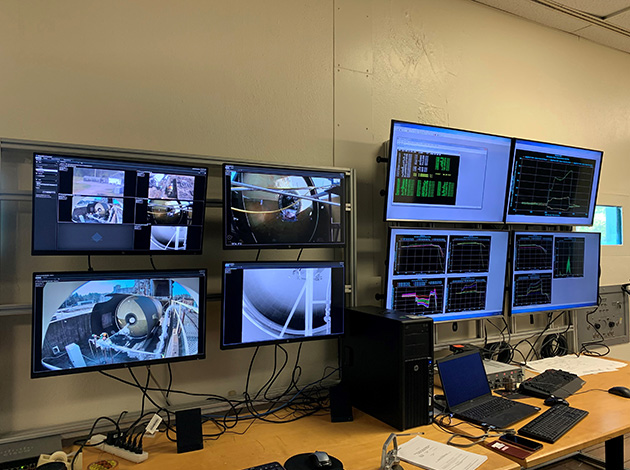
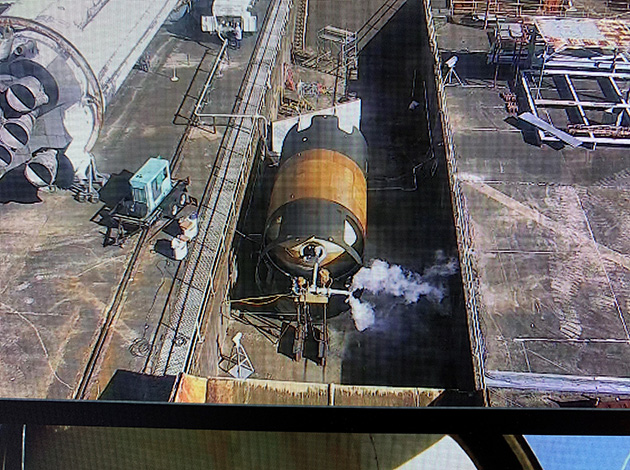
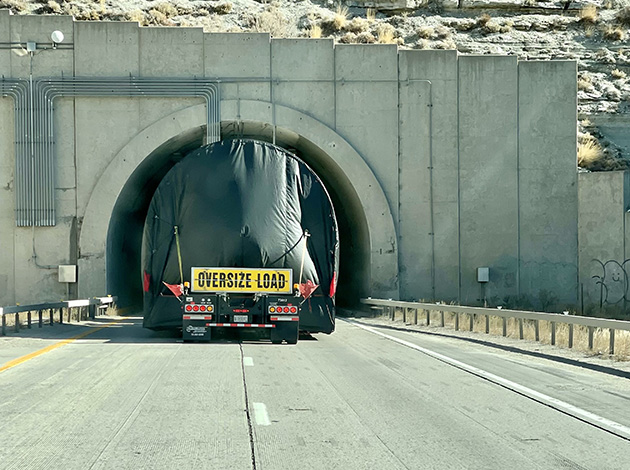
- Image 1
- Image 2
- Image 3
- image 4
- Image 5
Last October, a semi-truck began its slow crawl from Boeing’s Seattle factory down the Pacific Coast. Hauling a 30-foot-long composite cryotank, the truck crisscrossed the Southwest before heading east. Eight days and several thousand miles later—all driven at nighttime—NASA’s Marshall Space Flight Center in Huntsville, Alabama, came into view.
The cryotank’s arrival set the stage for a highly anticipated test campaign.
Beginning on Dec. 9, Boeing engineers loaded the tank into a NASA testing trench. With the engineers looking on from a remote viewing station, the tank was filled with cryogenic fluids until the internal pressure reached that of space launch and flight conditions. Sensors hooked onto the tank reported real-time strain and other data points. The tank was then emptied before additional cycles began. Each was completed without failure or leakage.
The trials, funded by DARPA and Boeing, validated the tank’s composite materials and fabrication methods—signifying that the technology is mature, ready, and reliable for use in aerospace vehicles.
A subsequent burst test a few days later pressurized the tank to 375% of expected operational loads—far beyond operational requirements—for insight into how failure eventually happens. Boeing engineers plan to cut the tank into pieces to learn more about the failure mode and design considerations needed to support the unique thermal environment for cryogenic fuels.
Boeing know-how
Measuring 4.3 meters in diameter (14 feet), the composite cryotank is similar in size to the fuel tanks intended for use in the upper stage of NASA’s Space Launch System rocket. It offers a number of advantages over tanks traditionally made of metal. The biggest is a weight savings of about 30 percent. With every pound of weight saved, another pound of payload can be delivered into orbit.
Boeing engineer Jon Embler, who has worked on versions of the tank since 2015, concedes that a layperson watching the initial tests might have found them “boring,” save for some frost that formed as liquid nitrogen coursed into the tank. And yet, he says, the significance of the results is anything but.
The automated fiber placement manufacturing processes and materials are the same ones used on the 787 fuselage, a testament to Boeing’s experience in building large, advanced composite structures. While other, smaller composite cryotanks are available for launch vehicles, their fabrication methods don’t scale efficiently to larger sizes and they require a metallic liner. Boeing’s 4.3-meter diameter composite cryotank uses a solid laminate wall and no internal metal liner.
“Boeing has extensive experience and knowledge from manufacturing more composite structures than the rest of the space launch industry,” Embler says.
Engineering a sustainable future
According to Brian Yutko, Boeing’s vice president and chief engineer for sustainability and future mobility, the benefits of composite fuel-tank technology extend beyond space and into applications where large amounts of cryogenic fuels need to be stored, like future hydrogen-powered aircraft. This could open the door to the use of cleaner fuels that curb the carbon impacts of aviation.
While this particular composite cryotank was designed for space, it has the capacity to hold 16,000 gallons of liquid hydrogen, the energy equivalent of about 3,700 gallons of Jet A fuel, which is typical of a regional jet sized airplane. This makes it a very credible scale for informing ongoing studies.
Using hydrogen aboard a commercial aircraft can eliminate in-flight carbon emissions, which has exciting potential. But it also introduces a number of important engineering and lifecycle sustainability challenges that Boeing continues to actively assess. Because hydrogen is not very energy dense by volume, most hydrogen aircraft will be larger and use more energy per passenger mile compared with equivalent Jet A or SAF aircraft. It also introduces certification, infrastructure, and operational challenges that Boeing is studying.
“Additionally, a complete lifecycle sustainability analysis is critical,” Yutko says. “Hydrogen is not naturally available by itself, so it must be produced (separated) from other compounds, which is energy intensive and increases upstream emissions using today’s production methods and energy grid. And when combusted on the aircraft, it results in non-CO2 emissions that have a large climate impact as well, which is a subject of ongoing study in the research community.”
Boeing has established a four-pillar strategy for meeting the aerospace industry’s commitment to achieve net zero carbon emissions by 2050, including fleet renewal, improved operational efficiencies, energy transition, and advanced technologies. While Boeing continues to make progress against every pillar, Sustainable Aviation Fuels (SAF) and their scale-up offers the largest potential to decarbonize aviation over the next 20-30 years.
“We’re using lessons learned from our five previous hydrogen demonstration flight test programs, along with this highly credible and large scale cryotank test, to inform the future of flight—in space and in the air,” Yutko says.