Rocket factory beams with innovation
Boeing team uses laser to enhance Space Launch System production
Boeing teammates at NASA’s Michoud Assembly Facility (MAF), “America’s Rocket Factory,” in New Orleans, Louisiana, are always looking for ways to innovate.
In that spirit of innovation, a three-person Boeing MAF team has programmed a laser tool to streamline and improve Space Launch System (SLS) rocket lapping operations — a process where technicians smooth product surfaces to a NASA and Boeing-required finish. When the two surfaces are bolted together, this creates a gas and liquid-tight seal.
Why it matters: Nearly the entire build of the SLS rocket requires lapping operations.
This improvement reduces this process from 20 minutes per part to one minute per part. With a minimum of 80 sandpaper cutouts required per job, the new process increases productivity by 95%.
- Ergonomic strains and safety risks are greatly reduced using this new method.
- The laser tool can be used on the core stages for Artemis missions II, III and IV, as well as the Exploration Upper Stage.
Callie Martin, team lead and Manufacturing Research & Development engineer, Chad J. Hatten, PC - Affordability Team engineer, and Kerry “Omarr” Ridley, Manufacturing Operations analyst evaluated the steps technicians have to take to perform lapping operations.
“This initiative has a lot to do with us three having the continuous improvement mindset and always looking to make things easier and better for Boeing,” Hatten said. “It was comforting to know that we had a collaborative cross-functional management team, and I want to give a shout out to those managers who helped us be successful, specifically to the memory of Kyle Sweet, our Supply Chain Manager, whom I dedicate our success to, as he was instrumental in the collaboration.”
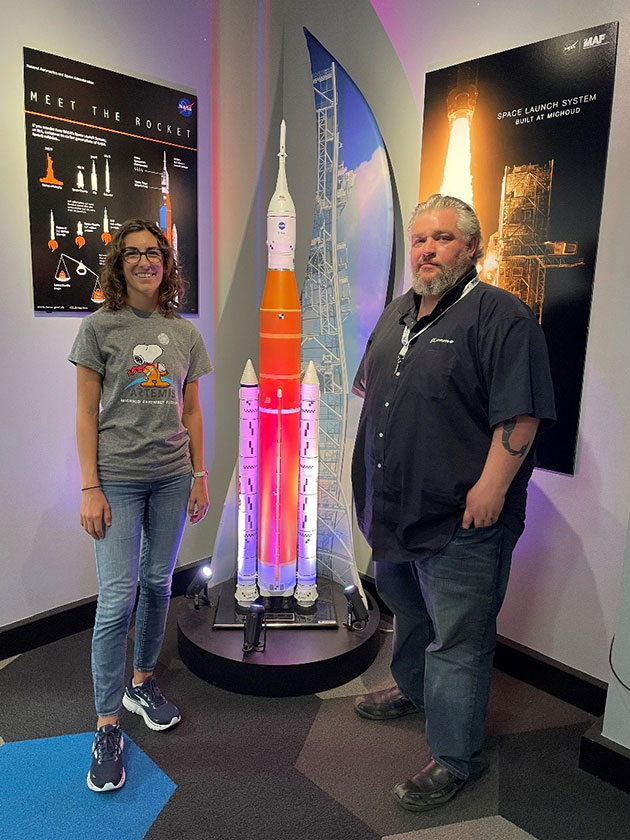
Lean mindset: “I talked to Omar about how difficult the process was with cutting out the sandpaper,” Martin said. By observing the process, seeking feedback from subject matter experts and reviewing time charge data, the group identified areas of improvement and researched ways to implement.
“I was very new, with only two months working for Boeing, so I didn’t know what types of equipment we had onsite for cutting. At my first engineering job, I worked with lasers a lot, which gave me the idea to use a laser for this application. I met Chad and he informed me that we have a laser cutter tool onsite, so we started doing testing from there. I’m grateful for the opportunity to get to know everyone on this project and see how excited they are to work together for an improvement that will help everybody.”
- The tool is in the prototype phase, but the SLS team plans to roll it out soon for all SLS technicians at MAF and the SLS team at Kennedy Space Center. The team is optimistic about the possibility of expanding usage of the tool to other programs across Boeing.
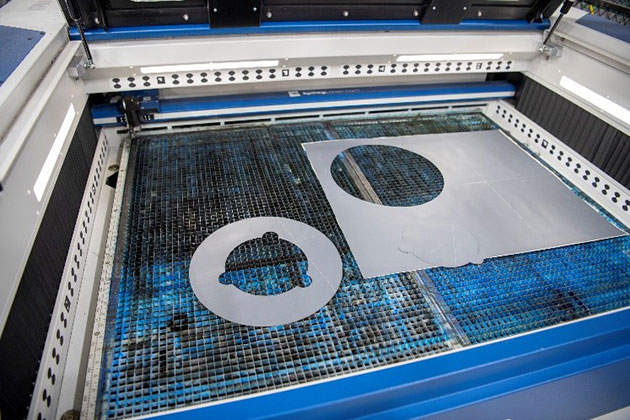
“This is something that will help the technicians not only do their job efficiently – but comfortably and safely as well,” Ridley said.
Recognition: Martin, Hatten, and Ridley were recently recognized with a Boeing Defense, Space & Security (BDS) Continuous Improvement Award based on this new process and laser-cutting tool.
NASA’s Space Launch System (SLS) rocket – the nation’s next-generation, human-rated rocket – will enable NASA’s Artemis program and will carry people and cargo to the moon, Mars and beyond. Boeing was selected by NASA to design, develop, test and produce the core stages, upper stages, and avionics suite for the SLS fleet of rockets. The first SLS rocket – featuring the Boeing-built Core Stage – successfully launched at 1:47 AM ET on November 16, 2022, as part of the Artemis I Mission. Production is currently underway for the Boeing-built core stages, upper stages (including Exploration Upper Stage) and avionics for future Artemis missions. Read more on BNN about SLS.
By Brent Duncan