Engineer’s skydiving enhances Starliner’s parachutes
Meet Ty Bowen, whose 2,000-plus skydives and decades of parachute know-how help prepare the Boeing spacecraft for flight.
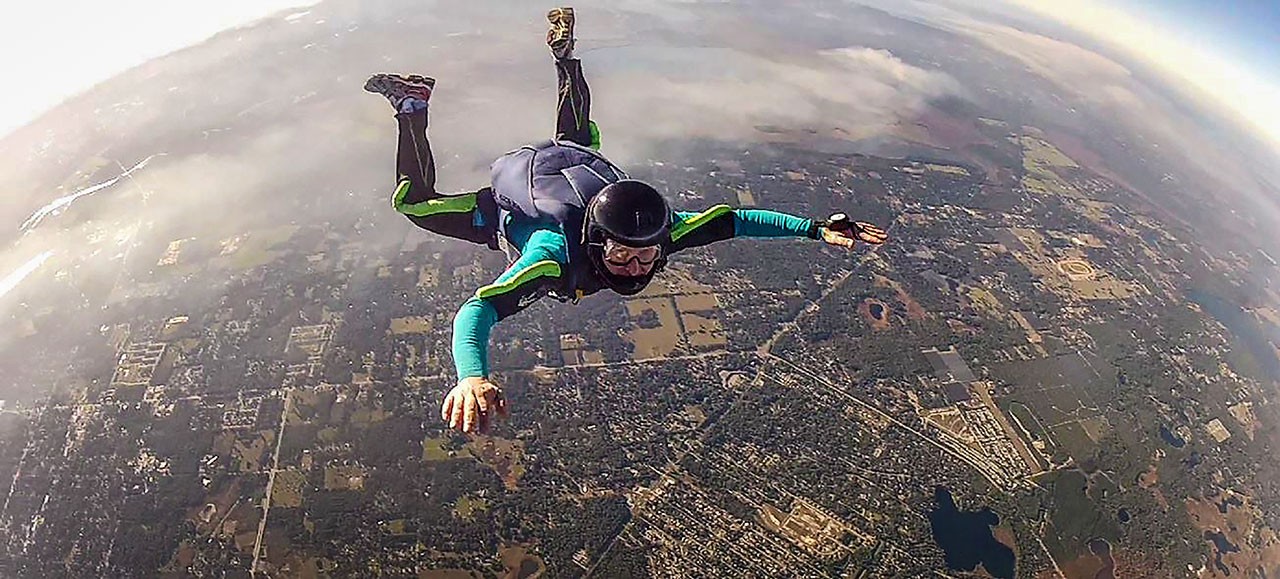
When Boeing engineer Ty Bowen skydives, his mind goes straight to the technical side of parachutes and how he can make them better and safer.
It’s been that way ever since his first jump in college, where the then-mechanical engineering technology major completed about 300 skydives.
More than 2,000 skydives later, that love of all things parachutes hasn’t stopped. As a parachute systems engineer for the CST-100 Starliner program, Bowen draws on a 32-year career spent designing, building, repairing, packing and maintaining parachute equipment. He has worked on a variety of parachutes, from solid rocket booster and orbiter drag chutes during the space shuttle program, to those used by sport and military skydivers.
A Federal Aviation Administration-certified master parachute rigger who has his name on several patents, Bowen has designs and parachute equipment he worked on that are being used by all U.S. military branches and many NATO allies across the world for special operations.
Hired by Boeing in January 2022, prior to the Starliner’s second Orbital Flight Test, for his expertise in large parachute systems, Bowen has been working to enhance the spacecraft’s parachute system. He has provided support for various testing and is lead for the Silver Team, which helps to recover the parachutes and stabilize the spacecraft after landings.
More recently, he has helped with new ways to strengthen and enhance the safety margins of the Starliner parachute soft links. These are the connection points between the suspension lines and the risers, which consist of strong webbing that connect the parachutes to the vehicle. His work has included developing prototypes in his workshop using industrial-size sewing machines he purchased during the shuttle era. Bowen designed and developed various prototypes and then tested them on a tensile test machine at the Starliner’s Commercial Crew and Cargo Processing Facility in Florida.
He and other Boeing team members worked with Starliner’s parachute supplier and NASA to find solutions.
“I love designing solutions,” Bowen said. “I started looking at how to improve and make the system stronger while minimizing the mass and volume changes to the existing configuration.”
His extensive experience also helped enhance other aspects of the parachutes related to packing and installation.
Fellow parachute systems engineer John Pike has known Bowen for more than 15 years, having worked with him on the NASA Ares program. Pike came to Starliner in 2017 after spending 18 years with the U.S. Missile Defense Agency. He also had his own rigging company, working with NASA and others designing, building and testing parachute systems for military and civilian tests. He learned parachutes in the British military working mostly for special operations forces.
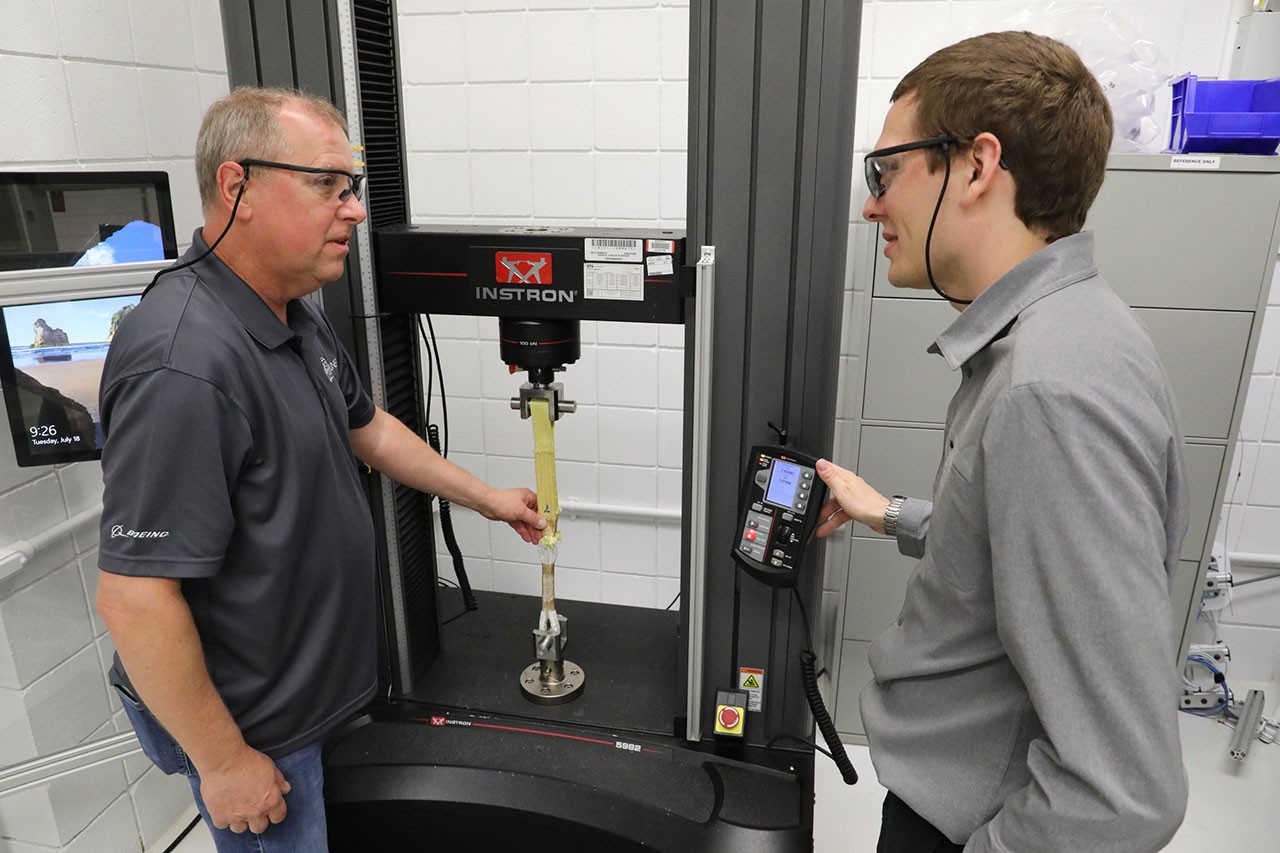
“We brought Ty onto Starliner and he has fit into the team really well,” Pike said. “His knowledge of materials and sewing has helped immensely. The soft links he made and tested helped us in going forward to our supplier. It has been easy to teach him the system, as he has extensive rigging experience and he picked it up quickly.”
Kirk Svartstrom, an integrated design team manager, said that in 2021 the Starliner team was looking to expand the Landing and Recovery team, specifically in the area of parachute systems.
“One name that continued to show up as we asked for recommendations from within the human spaceflight and military aircraft communities was Ty,” Svartstrom said. “Both his parachute expertise and his personal experience are just what we were looking for in a parachute expert.”
Prior to Boeing, Bowen worked for a parachute manufacturing company involved in inventing, designing, engineering and testing for sport and military customers. He worked for another private parachute company as a research and development manager and was a production manager who trained technicians in material handling, cutting, preparation and industrial sewing machine operations. He also served early in his career as a quality control inspector designing and implementing numerous upgrades to existing parachute harness and container product lines.
Bowen’s interest in parachutes started in 1990. Growing up in Ohio, he started taking private pilot flying lessons in college and met some skydivers. His interest quickly turned from learning how to fly planes to jumping out of them. While attending the University of Akron, he worked in between semesters and holiday breaks as an instructor at an indoor wind tunnel skydiving simulator in Tennessee.
“It’s definitely thrilling and it’s definitely an adrenaline rush,” Bowen said. “It was a fun, challenging thing to do that involved speed. When skydiving, you fall 120 miles per hour and you can dive downward and get over 200 miles per hour.”
Around the same time he started jumping, his mom joined him in the wind tunnel and then they did some actual jumps together. She later specialized in group canopy formation skydives and was on a team that set a record in the late 1990s for the largest women’s parachuting canopy formation.
He and his fiancée, who has over 30 years of sewing expertise on all components of parachute systems, have designed, built and tested various different manned and unmanned parachute systems. They were both instrumental in supporting the world-record highest-altitude skydive in 2014 (StratEx Space Dive), and their work is on display in the Steven F. Udvar-Hazy Center at the National Air and Space Museum in Virginia.
Bowen’s need for speed and use of parachutes doesn’t end with skydiving. He actively raced dragsters, which uses a parachute, for about eight years across the southeastern U.S. He hasn’t raced in 10 years, but still works on a car at home that he hopes to start racing again soon.
“Parachutes are lifesaving devices, whether they are on your body or on a vehicle. When you need it, you NEED it,” he said. “As a parachute system designer, builder, packer, etc., I work as if I’m the one using it.”
Working on crew vehicles and parachutes that will return crew safely from space, he added, “is the pinnacle of my career, and drives me to perform at my best.”