Pride in the Pegasus
A partnership of Boeing employees and hundreds of suppliers from across the country build the KC-46A Pegasus to be the world’s most advanced multi-mission aerial refueler for the U.S. Air Force and allies.
More than 37,000 American workers and 650 small businesses in 43 states supply the thousands of components needed to build the KC-46A Pegasus. From Branford, Connecticut to Stockton, California, each worker and business can take pride in fueling the global mission for the service members who depend on them.
“It’s personal.”
For Raytheon’s Mischa Dalcerri, Electronic Warfare Systems deputy director, supporting the KC-46 program is more than just a business imperative.
“As a family with active-duty service members, it's personal,” said Dalcerri, whose stepson serves in the Air Force. “Knowing the safety of the fleet is on our shoulders and part of our mission, it’s very important to us.”
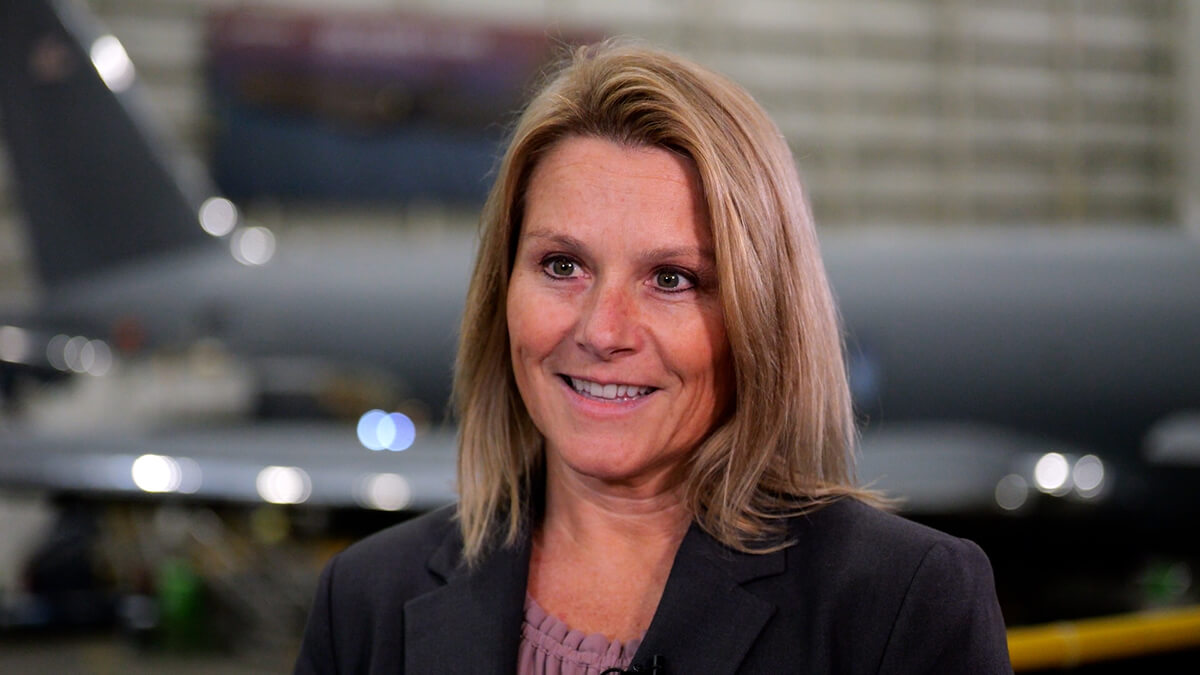
Raytheon, an RTX business, supplies the ALR-69A Radar Warning Receiver (RWR), which detects, identifies, and locates electronic threat signals to improve the aircraft’s situational awareness. The program is based in Goleta, California, and the receiver is assembled in Forest, Mississippi. About 800 Raytheon employees are split between the two sites.
Dalcerri noted that her teammates feel the same special connection to the Pegasus’ global mission for good reason.
“For a lot of our teammates, it’s really personal, as they’re former military,” she said. “We all want to do something noble and important, and this is the way we can all contribute to the safety of our nation as civilians.”
Commitment to quality
In Stockton, California, Applied Aerospace Structures – commonly known as AASC – plays in pivotal role in building parts for the KC-46A’s refueling boom.
AASC supplies composite fairings, rudders, and elevators for the boom.
“These lightweight honeycomb structures do a very good job of fulfilling a high-strength requirement that allows the boom to not only increate its longevity in the field, but also enables it to stay in the air for longer-duration missions,” program manager Auston Solway said.
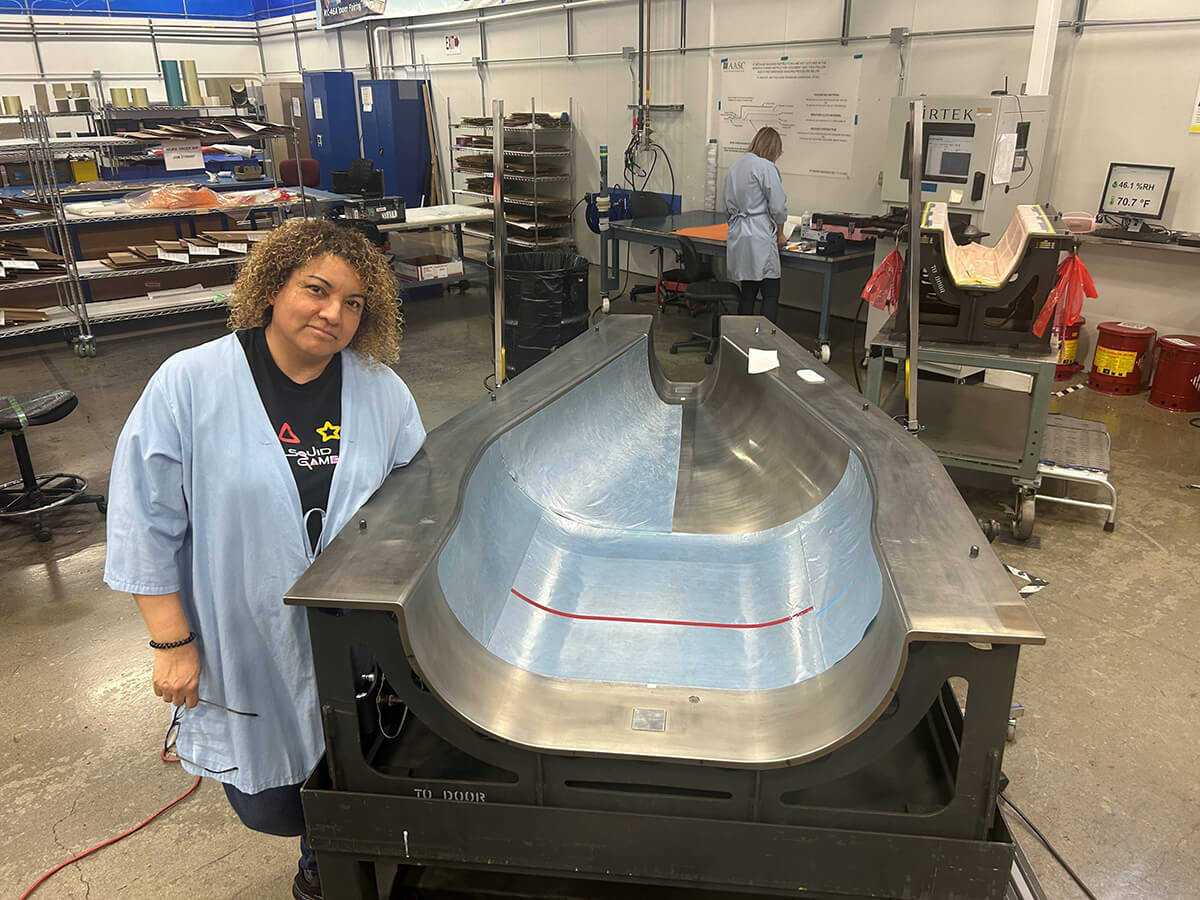
AASC employs more than 500 workers, with Solway noting that approximately 10 percent of the touch laborers are veterans. As for AASC’s success, Solway explained that focusing on crafting the quality products has been a key driver for business opportunities.
“AASC has been extremely successful because we align with our business’ protocol of really focusing on the quality side,” he said. “Focusing on quality not only allows us to make a great product, but it allows (Boeing) to continue to have a stable production environment, which also allows for our Air Force to have a stable production environment and support the fight where needed.”
Consistently delivering
When a receiver aircraft lines up behind a KC-46A, it relies on dual-mode LED lighting from Connecticut-based Oxley, Inc. to help guide it safely to the refueling boom. The lighting system operates in visual and infrared modes, allowing pilots to refuel in daylight or total darkness.
“Other tankers don’t have that capability,” Oxley business development manager Steve North said. “Our engineering team worked with Boeing engineers to establish it.”
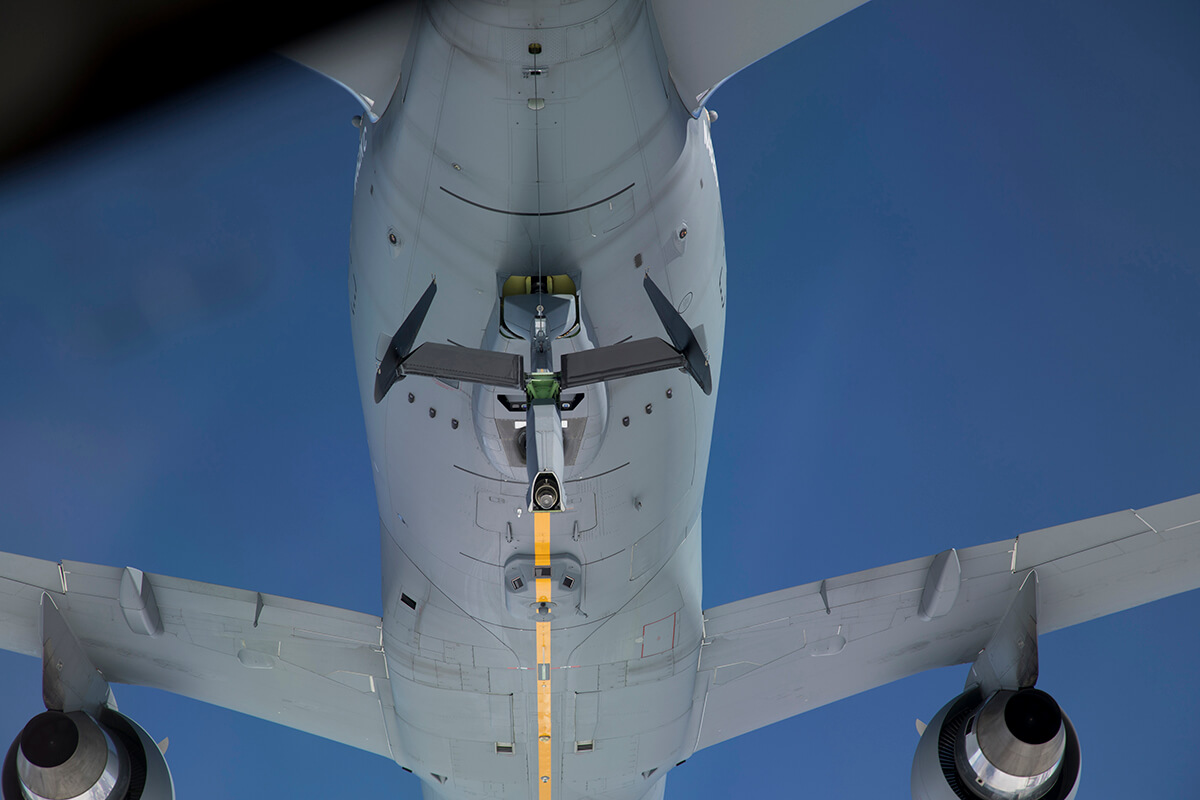
Having supported the KC-46 program for more than a decade, Oxley’s consistency in delivering a superior product for the U.S. military and allies is a critical part of its operation.
“On-time delivery is always a key part of our whole mission, so we flow all of the requirements down to our supply base to support that,” he said. “It really is a team effort with how we manage the product through its lifecycle. From contracts to future planning requirements – all of those steps are key in the way we manage this product and support the KC-46 mission.”
Fueling America’s tanker
Thousands of parts from hundreds of suppliers bring the KC-46A Pegasus to life on Boeing’s 767 production line in Everett, Washington. Standing on the mezzanine of the Everett Modification Center – where each tanker’s combat-ready defensive systems are installed – Fern Hernandez, Vice President of Supplier Quality and Performance for Boeing Defense, Space & Security, gave a nod to these businesses located across America for making the world’s most advance multi-mission aerial refueler possible.
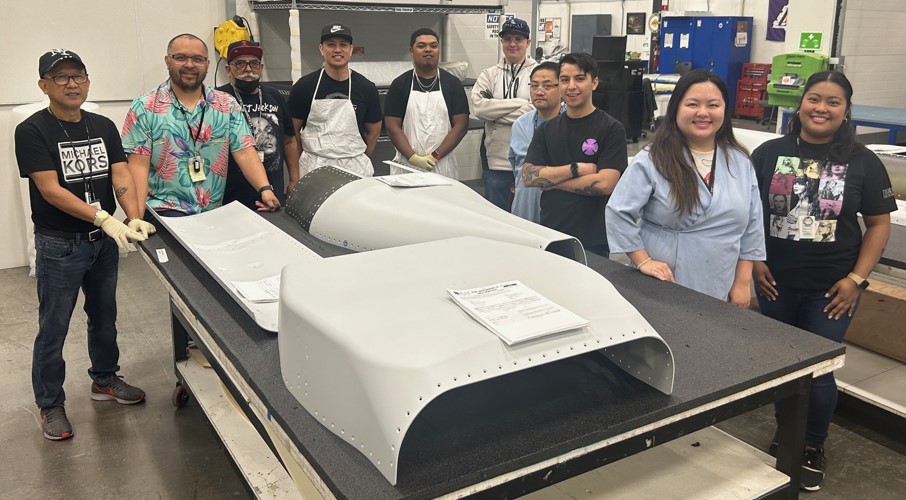
“Suppliers that we have for the KC-46 program are vital to our production system,” Hernandez said. “They provide thousands of parts every day to our facilities to ensure that the KC-46A is ready to be delivered on-time with the quality that we expect and also is expected from our customer.”
Hernandez stressed that Boeing’s partnership with these suppliers helps drive the same elements of quality and on-time delivery that are prevalent in successful companies such as Raytheon, AASC and Oxley.
“We have teams that are engaged with our suppliers out in the field and supplier quality representatives who work on a day-to-day basis to ensure that the engineering, the quality management system (QMS), and the products are made all the way through from start to manufacturing with the quality that’s expected,” he said.
“On-time delivery and quality are significant. The customer has an expectation that we deliver goods that meet their expectations and requirements, so our warfighters have products that are ready to go when they're ready to go, as well.”
Not subject to EAR or ITAR regulations.