Boeing ecoDemonstrator lands its first 10 tests
The program proves the environmental benefits of landing procedures among the 10 technologies it validated in latest testing.
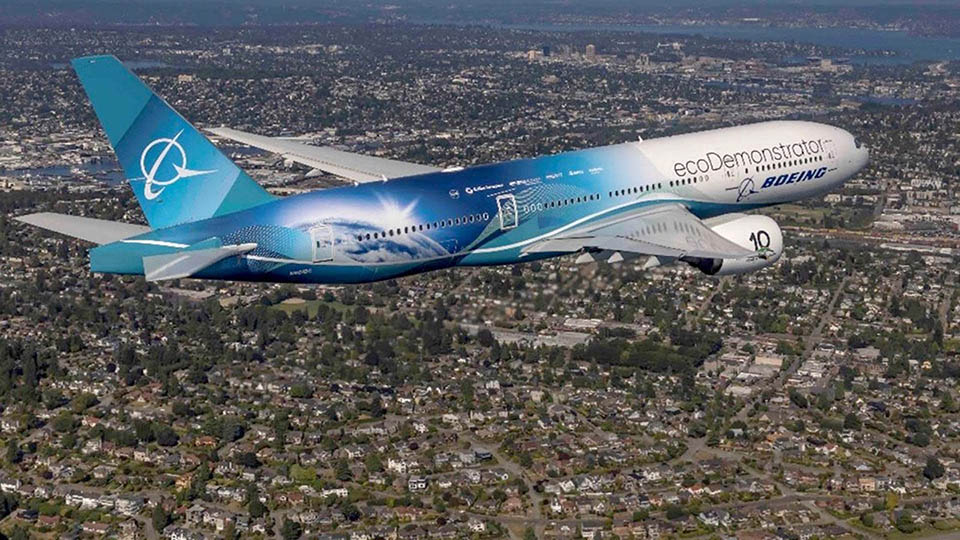
During several test flights this year, Boeing ecoDemonstrator pilots used operational procedures on approach to Boeing Field near Seattle to measure their environmental benefits – procedures like continuous descent approaches, less flaps settings and steeper glide slope.
- A team of Boeing’s Operational Efficiency and Flight Test engineers quantified the fuel savings and noise reduction using in-flight, noise and weather measurements combined with computer modeling.
- They observed that some of these measures, already adopted by the International Civil Aviation Organization, have the potential to save up to 800 pounds (363 kilograms) of fuel per landing on a 777-200ER (Extended Range) and reduce noise by up to several decibels.
Why it matters: “These operational procedures demonstrated a reduction in fuel use and noise, and the testing provided valuable real-world data to quantify those benefits and validate our models,” said Kirk Vining, Flight Operations functional chief engineer and a Senior Technical Fellow.
- Vining added that, because these procedures can require additional coordination with air traffic control, the ability to use them can vary at different airports.
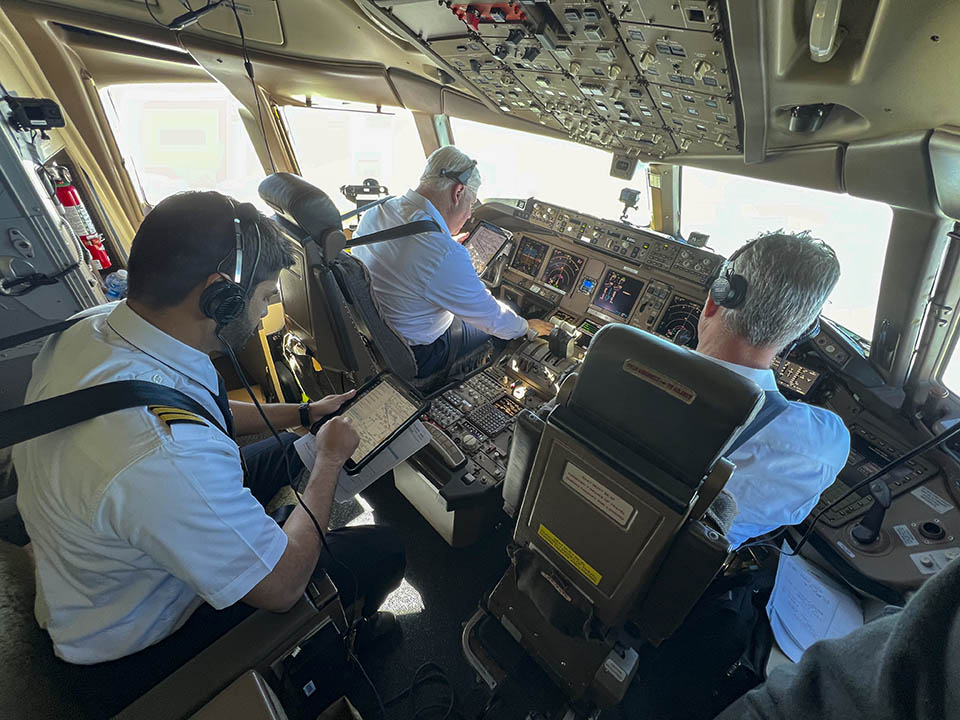
Catch up quick: This operational efficiency project was part of the ecoDemonstrator program’s first round of testing on its flagship airplane, collecting data on 10 technologies. Besides airport noise mitigation, the testing included other operational efficiency technologies, cabin interiors and several proprietary technologies:
- Enhanced capabilities of electronic flight bag application, Jeppesen’s updated FliteDeck Pro, such as an algorithm providing in-flight advisories to improve fuel consumption, and the ability to use real-time and historical data to predict taxi times.
- “Deep-dyed” digitally printed carpet that reduces weight by 120 pounds (54 kilograms) on a 787-9. It also uses less water, energy and produces less waste in the manufacturing process.
By the numbers: This year, the program has completed 85 ground and 15 flight test hours on its flagship airplane testing 10 technologies.
- Six proprietary technologies were also tested that could provide a competitive advantage if they progress onto Boeing products and services.
“By testing these 10 technologies, we collected 9,500 measurements from humidity sensors, video cameras, pressure transducers, and thermocouples,” said Rae Lutters, ecoDemonstrator program manager and chief engineer. “This provides valuable data, which we’ll be processing over the next several months.”
By Elisa Hahn
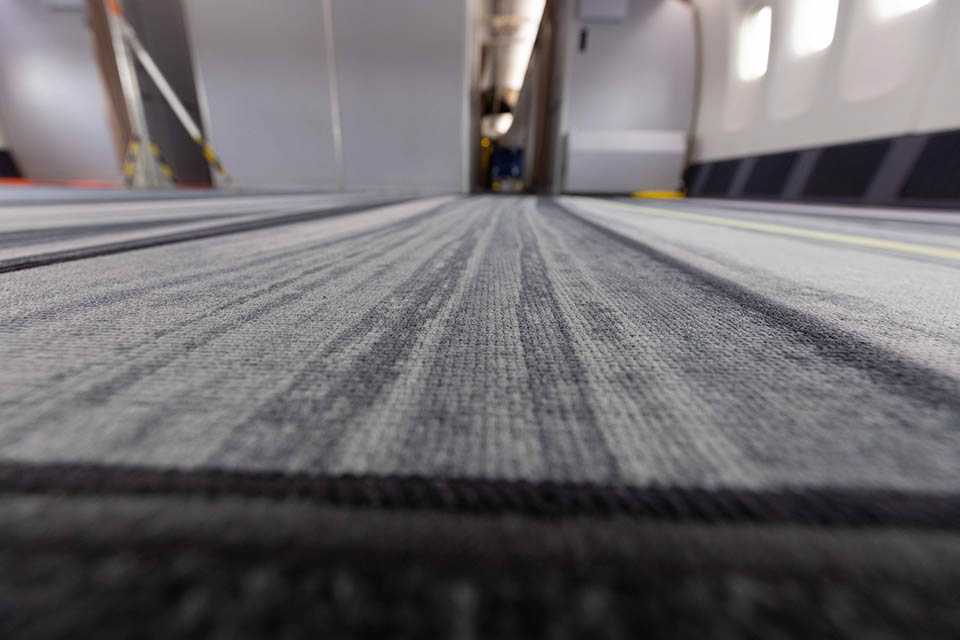